Plastic Injection Molding
From conventional injection molding to lastest injection molding technicals.
In-Mold Decoration
- Ultra-Durable
- All-in-One Process
- Cost-Efficient
- From 1 to 1,000 parts
Liquid Silicone Rubber Molding
- Heat & Chemical Resistant
- Flexible & Durable
- Precision & Cleanliness
- From 1 to 10,000 parts
Insert Molding
- Stronger Parts
- Simplified Assembly
- Cost-Efficient
- From 1 to 10,000 parts
Plastic Injection Molding Introduction
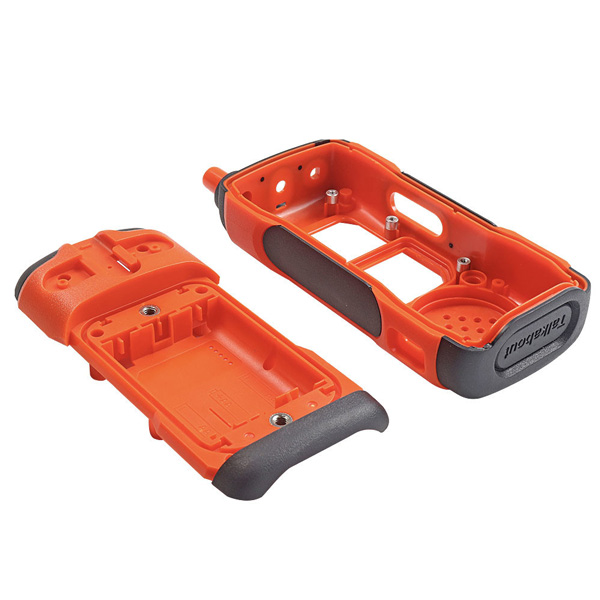
Plastic injection molding is a manufacturing process used to produce large volumes of identical plastic parts with high precision. It involves injecting molten plastic into a mold, where it cools and solidifies into the desired shape.
How It Works:
- Clamping – A two-part mold is securely closed under high pressure.
- Injection – Molten plastic is heated and forced into the mold cavity under high pressure.
- Cooling – The plastic cools and hardens inside the mold.
- Ejection – The mold opens, and the finished part is ejected.
Key Components:
- Injection Molding Machine (Clamping unit & Injection unit)
- Mold (Custom-designed steel or aluminum tool)
- Raw Material (Thermoplastics like ABS, Polypropylene, Nylon, etc.)
In-Mold Decoration (IMD) – Introduction
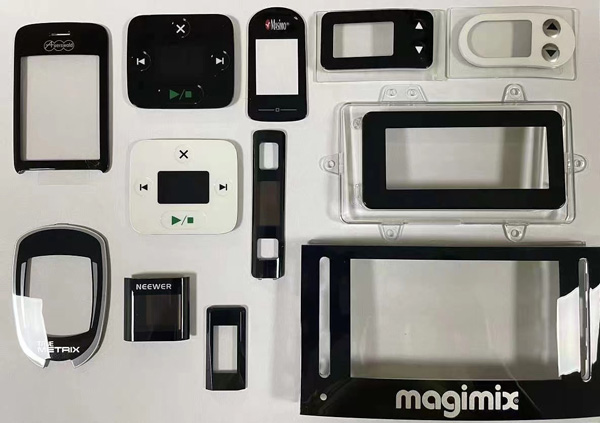
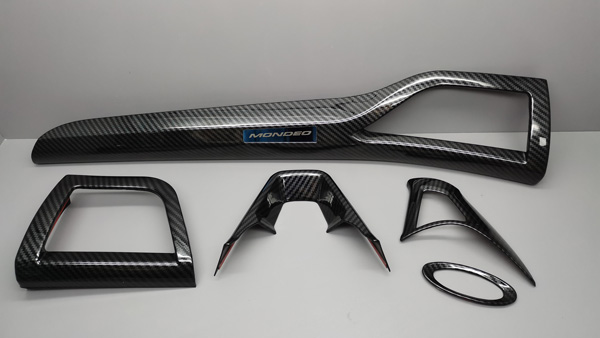
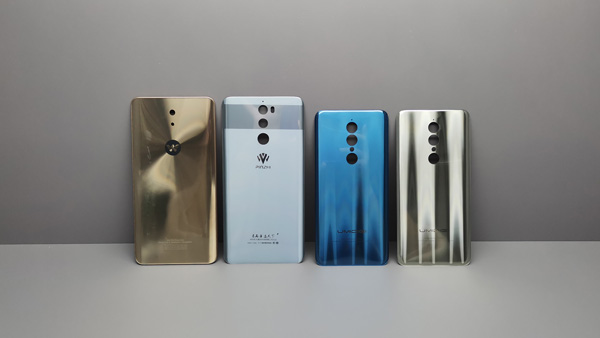
In-Mold Decoration Parts
Made by Longim
In-Mold Decoration (IMD) is an advanced manufacturing process that integrates decoration directly into plastic parts during injection molding. A pre-printed film or foil is placed into the mold before injecting molten plastic, resulting in a seamless, durable, and high-quality decorated surface.
Key Features of IMD:
- Single-Step Process: Combines molding and decoration in one operation.
- High Durability: Graphics are embedded within the part, resisting scratches, UV fading, and chemicals.
- Design Flexibility: Supports full-color prints, textures, metallic finishes, and even 3D effects.
Common Applications:
- Automotive: Dashboard panels, control buttons, logos
- Electronics: Smartphone/tablet casings, touchscreen bezels
- Consumer Goods: Appliance panels, cosmetic packaging
- Medical Devices: Durable, sterilizable labels
Advantages Over Traditional Methods (Painting/Pad Printing):
✔ No post-processing needed (reduces cost/time)
✔ Superior scratch/weather resistance
✔ Lightweight & seamless integration
IMD is ideal for high-volume production of parts requiring premium aesthetics and long-lasting durability.
Incredibe Extremely
Easy to Collaborate with Globally, and Delivers Your Parts on Time.
A reliable partner that makes collaboration effortless and delivers precision parts on time, every time.
Case Studies
Parts & Products
While these examples highlight our plastic injection molding capabilities, they represent just a fraction of our expertise. With an extensive portfolio spanning consumer electronics, automotive, and medical applications, we’ve successfully delivered complex, precision-crafted components that consistently meet the most demanding quality standards and customized specifications. Our advanced tooling technologies and cross-industry experience position us to bring the same level of excellence to your project – let’s discuss how we can exceed your expectations.
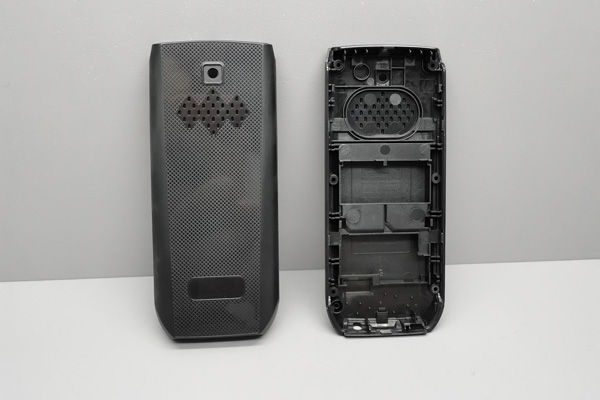
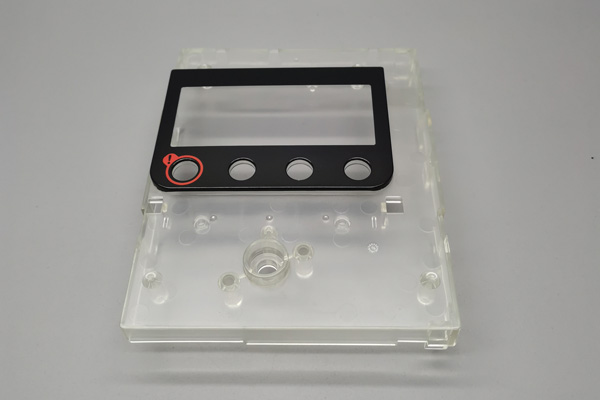
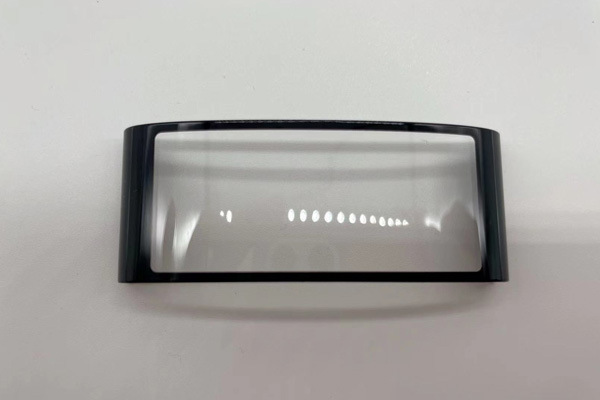
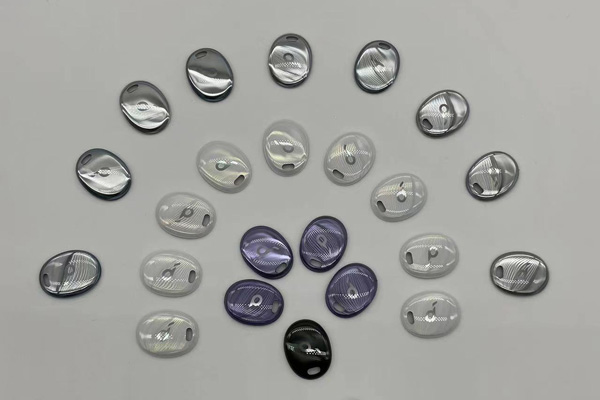