Sheet Metal Fabrication
From Flat Sheets to Flawless Forms — Fast & Precise.
Bending
- High Precision
- Cost-Effective
- Material Efficiency
- Versatility
Forming
- Complex Shapes
- High Strength Retention
- Smooth Finishes
- Mass Production
Cutting
- High Accuracy
- Flexibility
- Fast Production
- Minimal Distortion
Sheet Metal Services
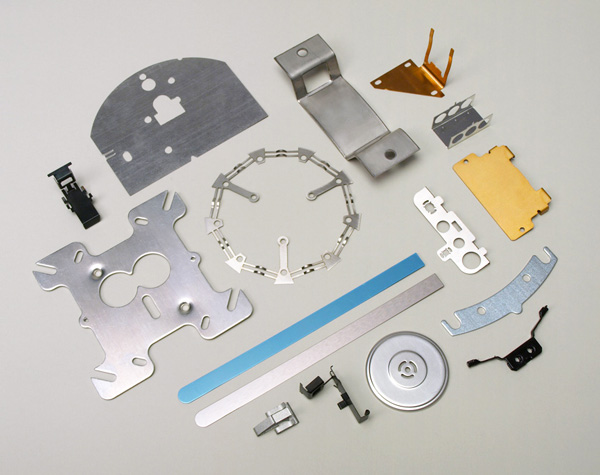
Sheet metal services encompass a range of manufacturing processes designed to cut, bend, form, and assemble metal sheets into functional components and structures. Using advanced techniques such as laser cutting, CNC bending, stamping, welding, and assembly, these services deliver high-precision parts for industries like automotive, aerospace, construction, electronics, and HVAC.
Key Capabilities Include:
- Cutting: Laser, plasma, and waterjet cutting for intricate designs with tight tolerances.
- Bending: CNC press brakes for accurate angles and complex geometries.
- Forming: Stamping, deep drawing, and roll forming for custom shapes.
- Finishing: Deburring, powder coating, anodizing, and polishing for enhanced durability.
- Assembly: Welding, riveting, and fastening for complete fabricated solutions.
Whether for prototyping, custom fabrication, or large-scale production, sheet metal services offer cost-effective, durable, and high-performance solutions tailored to meet stringent industry standards.
Extremely
Easy to Collaborate With and Delivers Your Parts
A reliable partner that makes collaboration effortless and delivers precision parts on time, every time.
Case Studies
Parts & Products
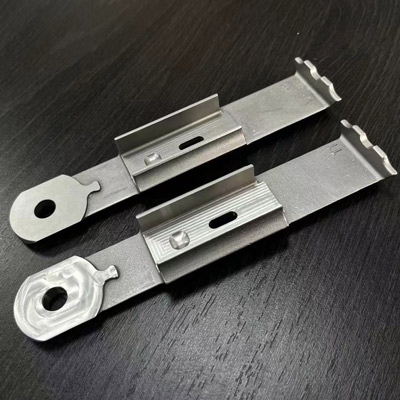
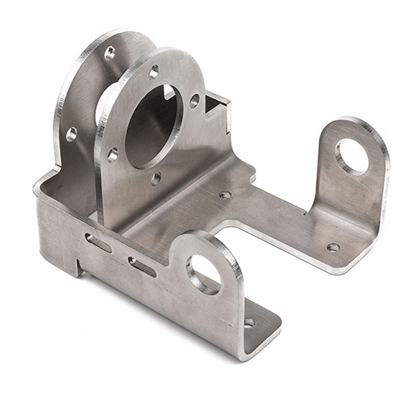
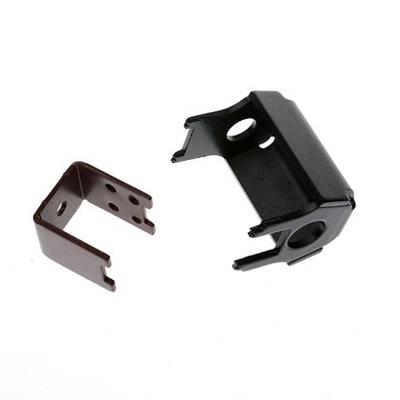
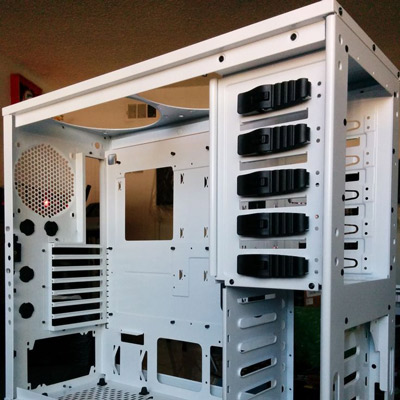